New headquarters in Istrana (Treviso)
After long and demanding months on the construction site, we are happy and proud to announce the opening of the new headquarters in Istrana, in the province of Treviso.
It is a newly built, designed specifically for the laser cutting industry: 6 dedicated machines in an area of 18000 square meters, an international reference for laser cutting of pipes and profiles.
We thank all the collaborators, workers, professionals and the companies that have supported and endured us in the last year and a half, without you it would not have been possible. Find out more about the new location>
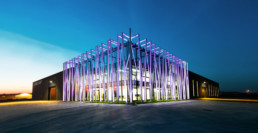
Building with steel: beautiful, easy and convenient
From the magazine: INSPIRED FOR TUBES, April 2016, Number 22:
Laser cutting of small diameter (<6”) and medium size tubes (<12”) is now a universally accepted industrial process; but is laser tube cutting and specifically the use of a fiber laser, useful when it comes to large diameter tubes? To find out the answer to this question, let us go to the Venetian hills in Italy, in the Prosecco wine region, to a company called Tubilaser S.r.l. For more than 15 years, Tubilaser has been a supplier of structural steel tubing and laser cut tubular components.
Tubilaser serves a wide variety of industries; construction (bridges and stadiums), agricultural machinery manufacturers, ski-lift structures for ski resorts, interior design and architectural elements, general fabrication, etc. In short, their customers can be anyone that uses laser cut tubular components. Tubilaser initially purchased BLM GROUP’s laser tube cutting technology as a way to differentiate themselves from other fabricators. According to Guido Bonaldo, owner of Tubilaser, “it was a way for us to be able to offer our customers better quality components at a lower cost”.
The decision to use the laser cutting process for large dimension tubes was in part a logical decision because it allowed Tubilaser to satisfy their customers’ requirements but it was also a result of entrepreneurial intuition that Guido Bonaldo had nearly 15 years ago, much ahead of its time. He rightly realized the potential advantages offered by laser cutting process, even in cutting large tubes. These advantages weren’t as obvious at the time he made the investment. “Initially all the customers treated my decision to invest such a large sum for a machine as sheer madness” says Bonaldo referring to his decision to buy the LT20. “In the early days, we did not receive any drawings requesting we quote on large components or structures. We had to work hard with our customers engineering departments to convince the designers about the advantages of using the laser cutting process. These advantages were well-known for smaller tubes but it took some time to convince the market that the same advantages were valid for larger, heavier tubes”.
Slowly the customers began to realize the benefits of laser cutting and started to implement innovative design solutions for their parts. Now, even for simple applications, the laser cutting process is automatically assigned. Flavio Colusso, Tubilasers’ production manager, explains it this way. “The advantage does not lie in the automation of the manufacturing process for a single component, but they cover the entire production process for a given project and that results in the overall lower costs compared to the traditional processes” says Flavio. To explain his point he gives this example.
“Let us consider two 40 feet long, large diameter round tubes. These tubes are to be end-cut to form a 90° joint between them and they also have other pockets to be cut along their length where additional tubes are to be inserted to form a tubular structure. Now you will appreciate that these pockets have to be cut with correct orientation with respect to the end-cuts; a small error, even of one degree in terms of orientation, will cause considerable mismatch at the other end of the tube. Such errors are common when fabricating with traditional manual processes. The time required to rework the parts (often in the field) to correct these errors can be almost infinite. The LT JUMBO family of laser tube machines can produce these types of large tubes in a single, completely automatic cycle with an accuracy and repeatability that cannot be matched by the old manual processes.
"With traditional methods, the total time (and hence cost) required to produce a given component can’t be determined in advance because it depends upon a number of factors, the most important of which is the operator skill"
"With traditional methods, the total time (and hence cost) required to produce a given component can’t be determined in advance because it depends upon a number of factors, the most important of which is the operator skill"
Filippo Bonaldo
“An example of one such successful project was the fabrication of complex tubular structures for railroads. These structures are installed along a railway line and are used to hang signals and other indications for trains. These tubes were laser-cut and then sent to the site, ready to be assembled. No further adjustments or any kind of rework was required during their assembly and the structures were assembled like a puzzle” says Bonaldo. He continues and touches another important aspect; “The operator skills in the traditional processes are not the same as they were once upon a time. In the past, an operator was capable of producing a component on his own once you gave him the drawing. New workers don’t have the same skill set. Any mistakes made are very costly because either you have to spend a lot of time for rework and repair or scrap everything and start anew. Since material cost for large dimension tubes is very high, one can’t afford to do this”.
Using a fiber laser on the LT14 machine was also not an obvious choice because the machine was designed to be used for large diameter tubes with thick walls and we all know that the fiber lasers offer their best performance in terms of higher cutting speed when used to cut thinner materials. The fiber laser was chosen for its overall lower operating costs. “The tubular construction and agricultural machinery sectors are extremely cost sensitive. Fiber laser technology with its lower energy consumption (and hence lower installed power requirements) and lower maintenance helps to reduce the cost per piece. It also adds the capability to cut other materials. This expanded capability is an important factor for any tube fabricating job shop. These advantages amply offset the small compromise that we have to accept with the quality of cut surface obtained” says Bonaldo. In fact, compared to an installation with a CO2 laser, the electrical power requirement is almost half, there is practically no maintenance required on the laser resonator because there are no moving parts in the fiber laser, there is no chain of mirrors to guide the beam and hence no question of their alignment, cleaning and maintenance. With a CO2 laser all these maintenance activities result into stoppage of machine and loss of production. In addition to that, fiber laser has an additional stand-by power module inside the fiber laser that kicks into action in case one of the operating modules should have some problems.
The use of fiber laser technology compels the machine manufacturer to completely enclose the working area to ensure operator safety. On the LT20 the laser cutting process is viewed via video cameras installed in the working area. Bonaldo considers this aspect as a plus. “Since the working area is totally enclosed, the machine manufacturers have to pay extra attention to make certain the machine operation is more reliable and capable of resolving eventual hiccups in an automatic manner, as much as possible” says Bonaldo. An interesting point of view!
We can conclude that the challenge of using laser cutting process for cutting large dimension tubes has been overcome. There was some reluctance in the beginning but now Tubilasers’ customers have understood the advantages of having accurate, high quality components that can be easily assembled and welded on site and hence the laser cutting process for such components has become their new standard. The designers working in this industry have also learned the potential new design freedoms offered by this technology, and they have started to use it freely to design innovative structures that are aesthetically pleasing. Contact us for more informations >
The laser conquers new applications
Taken from the INSPIRED FOR TUBES magazine (March 2012, Issue 16):
The potential advantages of using lasers to process metal tubes are now well-known in many fields of application. In particular, when working with large and therefore thicker tubes, the possibility of precision processing has paved the way for new construction solutions.
The potential advantages of using lasers to process metal tubes are now well-known in many fields of application. The automated process condenses the various processing stages into a single stage, whilst also boasting precision and the possibility to create virtually limitless new processes. All this is now well-known and has been substantiated by numerous applications in the furniture, mechanics and automotive sectors, and more generally, by all applications that require small or medium-sized tubes, i.e. tubes with a maximum diameter of 200 mm. However, what happens when larger tubes are required? Can the same logic be extended to applications that require larger pipes?
Process automation and precision
If, for example, we consider the fact that the ADIGE-SYS LT Jumbo 20 system can currently process tubes with a maximum length of 18 m, maximum thickness of 16 mm and maximum diameter of 508 mm, it becomes immediately evident that a fundamental problem to be solved is the way in which these tubes–which can each weigh up to 35,000 kg–are handled. There is a clear advantage to a laser system which, by starting with a certain number of aligned bars, is able to individually load each bar on the processing line, fully process them and unload the finished workpieces in an orderly manner.
Even when working with these dimensions, the possibility of precision processing paves the way for new construction solutions that can be used in areas such as the agricultural machinery or mechanical construction sectors (e.g. cranes, warehouses, etc.).
"The possibility of creating structures with joints instead of simple supports, facilitates assembly by eliminating the possibility of human errors which would be particularly expensive"
"The possibility of creating structures with joints instead of simple supports, facilitates assembly by eliminating the possibility of human errors which would be particularly expensive"
However, when working with large and therefore thicker tubes (up to 16 mm), lasers boast an additional advantage compared to the traditional technologies, and that concerns the so-called heat-affected zone. This is the area immediately adjacent to the cut in which the heat generated during the process, causes the material’s characteristics to be significantly altered; this area is extremely small and negligible as a result of laser processing, whilst it is unacceptable (and must therefore be subsequently removed) when the tubes are cut via the more traditional thermal technologies.
Think of the support structures found in ski resorts or theme parks (e.g. roller coasters), where the sturdiness of the structures is an essential safety element. In conclusion, the answer to the earlier questions is a definitive yes. There are numerous, different reasons why laser processing large tubes is suitable for many sectors and fields of application, and it is on this fact that Tubilaser has based its core business: contact us for more information>